物流システムのコラム
COLUMN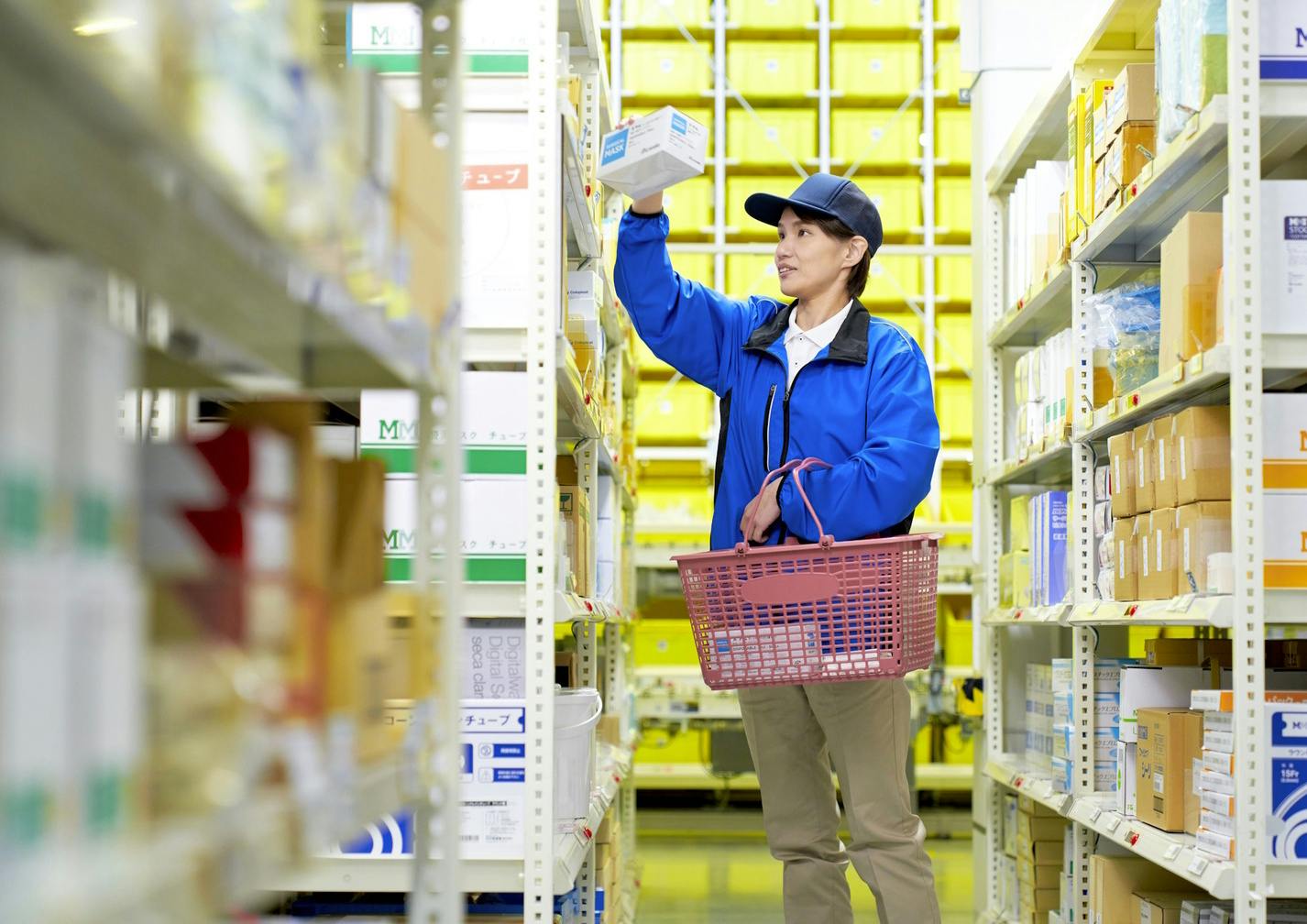
ピッキングとは? 作業工程・種類から効率化するポイントを紹介
ピッキングとは、伝票や注文書、指示書などの内容に沿って、指定の品を取り出す作業を指し、入荷から仕分け、出荷まで庫内作業のさまざまな工程で発生します。ピッキングでは、商品の取り間違いなどのヒューマンエラーが生じる場合もあるため、マニュアルの整備や倉庫内のレイアウトの見直しなど、対策を練ることも重要です。この記事では、ピッキングの意味や主な作業内容、課題、ピッキング業務を円滑に行うための改善ポイントなどをご紹介します。
倉庫・工場におけるピッキングとは
倉庫・工場内において、ピッキングは入出庫・仕分けなど、各工程で発生する作業で、特に近年では物流が多頻度小口化しているため、庫内作業におけるピッキング工程は増加しています。
ピッキング作業を行うにあたって、特別な資格やスキルは必要ありませんが、円滑にピッキングを進めるために、倉庫内の荷物の場所を把握したり、正確に指定の荷物をピックアップしたりすることが求められます。
ピッキングの主な作業内容
先述のとおり、ピッキングでは、倉庫や工場内に保管されている品を、伝票や注文書、ピッキングリストに記載された情報に従って集めます。ピッキングが円滑かつ正確に行われなかった場合、次工程に大きな影響を与え、スケジュールどおりに荷物が届けられないこともあるため、ピッキングは庫内作業の中でも特に重要であるといえます。
ピッキングで扱う商品の種類
ピッキングで扱う荷物は、工場で使用する部品や仕掛品のほか、日用品や雑貨、電化製品、書籍、食品、医薬品など多岐にわたり、倉庫や工場によって、扱う荷物の大きさや重さ、数量はさまざまです。ピッキングは基本的に人の手で行われますが、荷物の大きさや重さによっては、フォークリフトを利用する場合もあります。
ピッキングの課題
ピッキングは基本的に人の手で行われるため、荷物の取り間違いや数量間違いなどのヒューマンエラーが生じることがあります。ここ20年間では出荷重量が2割以上減少している一方で、出荷件数は6割以上増加しています。ここから流通の多頻度小口化が進んでいることがうかがえます。
取り扱う荷物の数が増えるにつれて、ピッキングの業務量は増えるため、限られた業務時間内で、より多くの荷物を素早く正確に集める体制や倉庫環境を整えることが課題とされています。課題については、このあと詳しくご紹介しています。
ピッキングの種類
トータルピッキング(種まき方式)
トータルピッキングは、複数のオーダーを合算し、種類ごとに荷物を集めるピッキング方法で、種まき方式と呼ばれることもあります。トータルピッキングは、SKUが少なく出荷件数が多い、少品種大量出荷に適しており、同一の品を複数の出荷先へ届ける際におすすめの方法です。SKUとは「Stock Keeping Unit」の略で、品種だけでなく、例えばアパレルの場合、色やサイズなど(Mサイズのブラック、Sサイズのブルーなど)でさらに細分化したものの単位を指します。
トータルピッキングでは、複数箇所からオーダーが入った部品や商品を種類ごとにまとめて集めることができるため、スタッフの移動距離やピッキング時間を削減しやすい点が特長です。ただし、トータルピッキングでは、荷物を集め終わった後、仮置き場や仕分け場で出荷先別に仕分けする作業が発生するため、注意が必要です。
シングルピッキング(摘み取り方式)
シングルピッキングは、オーダーごとに1梱包にまとめて荷物を集めるピッキング方法で、オーダーピッキングまたは摘み取り方式と呼ばれることもあります。シングルピッキングは、SKUが多く出荷件数が少ない、多品種少量出荷に適しており、ECサイトの通販などで多く用いられています。
シングルピッキングは一つ一つのオーダーごとに荷物を集めるため、作業内容がシンプルであり、ヒューマンエラーが起きにくい点が特長です。しかし、オーダー数によっては作業者の庫内移動が多く発生することもあるため、作業者への負荷や作業時間の増加につながります。
マルチオーダーピッキング
マルチオーダーピッキングでは、複数オーダー分の部品や商品を集めながら、仕分けを同時に行うピッキング方法です。あらかじめ出荷先の数に応じたカートやコンテナを用意し、部品や商品をピックアップしながらオーダー内容に合わせて投入することで、作業効率の向上が期待できます。
例えば、「A商品×3、B商品×10」「A商品×5、B商品×3」という2件のオーダーがあった際、スタッフは2つのカートを用意し、A商品を8個取り出しながら、3個と5個をそれぞれのカートに仕分けします。同様に、B商品も13個取り出し、その場で10個と3個に仕分けします。
マルチオーダーピッキングでは、仕分けを同時に行えるため作業効率は上がるものの、仕分けミスなどのヒューマンエラーに注意が必要です。
倉庫・工場におけるピッキングの課題
ピッキングミスの発生
ピッキングでは、主に部品や商品の種類や数を間違えたり付属品を取り忘れるといったピッキングミスが発生しやすい点が課題として挙げられます。ピッキングミスはヒューマンエラーとなるため、完全に防ぐことは難しいでしょう。
しかし、ピッキングミスを最小限に抑えるためには、個人のミスによるものなのか、ミスが起こりやすい倉庫環境であるか、業務マニュアルがわかりづらいのかなどの現状把握を行い、問題に対して改善を繰り返すことが大切です。
探すのに時間がかかる
ピッキングリストや商品番号が確認しづらい場合や、保管場所が離れた位置やわかりづらい場所にある場合、入庫時の格納ミスにより保管場所が誤っている場合など、さまざまな原因によりピッキングする際の「探す」時間がかかってしまうケースがあります。また、商品がロケーション管理されていない倉庫の場合は、さらに時間を要してしまうでしょう。
季節波動への対応
需要期・繁忙期ではピッキングの作業量が増加したり、追加スタッフなどの人員拡充が必要になることがあります。
また、時間外労働の発生や、通常より倉庫内を動き回ることが多くなることから、スタッフの肉体的・精神的な負担も増加する傾向があります。季節ごとの需要に変化があり繁忙期が発生する倉庫の場合は、作業量の増加によるミスの発生や出荷遅れ、人員補充やそのスタッフへのレクチャー、時間外労働の発生などが課題となります。
作業者へのトレーニング
ピッキングする品が初見であったり、ピッキングの作業手順が複雑であったりする場合、新人やパート・アルバイトスタッフの育成に時間がかかってしまうことがあります。そのためピッキングマニュアルの整備やわかりやすいロケーション番号の表示など、誰でもわかりやすくピッキングできる環境を整える必要があります。
ピッキング作業の改善ポイント
倉庫のレイアウトやロケーションを見直す
スタッフ一人ひとりの業務効率を上げるためには、スタッフが倉庫内を移動しやすくなるよう、適切な作業動線を確保することが重要です。そのために、倉庫内の作業スペースや保管スペースといったレイアウトが、業務を進めるにあたって無駄な移動が発生しない配置にできているか見直すとよいでしょう。
また、ピッキングをする際、部品や商品のロケーション管理が複雑であると、スタッフが探す・取り出すことに時間を費やしてしまう可能性があります。ロケーションを設定する際は、棚の区別がつきやすくなるように番号を振ったり、どこに配置されているのかをすぐに把握できるようルールを設定したり、棚からそのまま取り出せるように開梱しておいたりするなどの工夫が必要です。
在庫管理システムや倉庫管理システムを導入
在庫管理システムや倉庫管理システム(WMS)を導入することもピッキング業務を効率化させることにつながります。在庫管理システムは、倉庫内の在庫数をリアルタイムで把握することができ、倉庫外で扱っている在庫の管理も行えます。一方で、倉庫管理システムは、在庫管理に加えて、入出庫の作業指示や倉庫内の進捗状況など倉庫業務に関するさまざまなデータを管理し、倉庫業務を効率化させることができます。
検品作業の徹底
商品の取り間違いといったヒューマンエラーを最小限に抑えるために、検品を徹底することも大切です。ピッキング工程だけではなく、出荷までの工程の中で再度検品することで、正確性を維持できるようになります。
コミュニケーションを活発化
倉庫業務は、個人で黙々と作業を進めるイメージを抱いている人も多いのではないでしょうか。しかし、仕分け時や梱包時などは、それぞれの業務を行うスタッフと連携を取り、正確かつ迅速に商品を受け渡す必要があります。特にオーダー数が増える繁忙期は、多くの品を素早く出荷する必要があるため、ミスを最小限に防がなければなりません。
ヒューマンエラーを防ぐためにも、日ごろからさまざまなスタッフとコミュニケーションを取り、それぞれのスタッフがどのように作業を進めているのかをある程度把握しておくことも大切です。
ロボットや自動倉庫システムの導入
業務量に対してスタッフ数が足りない場合や、作業スピードが追いつかない場合は、自動倉庫システムを導入することもおすすめです。オカムラが提供する「オートストア」や「ロータリーラックH」では、荷物の入出庫を自動で行えるため、作業者が定点でピッキングできるGTP(Goods To Person)を実現し、業務効率の向上が期待できます。
さらに、ピッキングを自動で行えるロボットを導入し、人の手に負えない業務をサポートしてもらうこともできます。オカムラの「ライトピック」は事前のティーチングやマスター登録をすることなく自律ピッキングができます。
まとめ
この記事では、ピッキングの意味や主な作業内容、課題、ピッキング業務を円滑に行うための改善ポイントなどをご紹介しました。人の手でピッキングを行う場合、商品の取り間違いや数量ミスといったヒューマンエラーは必ず生じるため、チェック体制の強化や、スタッフが作業しやすい倉庫環境の整備が必要です。自社の状況や予算に合わせて、ピッキング業務を自動化できるロボットや自動倉庫システムを導入するのもおすすめです。
ピッキングロボットや自動倉庫製品については、オカムラまでご相談ください。
製品情報やお問い合わせはこちらから。
オカムラ 物流システム事業サイト